The Ultimate Guide to Understanding Aluminum Deep Drawing
Aluminum is a non-ferrous metal commonly used in different applications. Manufacturers often utilize aluminum for various products because it is inexpensive, non-toxic, recyclable, and machinable, making it ideal for deep drawing. However, it is crucial to understand aluminum deep drawing to exploit its full potential of aluminum.
Aluminum deep drawing is a specialized manufacturing process critical to various industries, including automotive, aerospace, electronics, and household appliances. Its significance lies in its ability to transform flat sheet metal into complex shapes with great precision and efficiency. This comprehensive guide aims to demystify aluminum deep drawing, covering everything from its fundamental principles to advanced techniques and applications.
Understanding Aluminum Deep Drawing Fundamentals
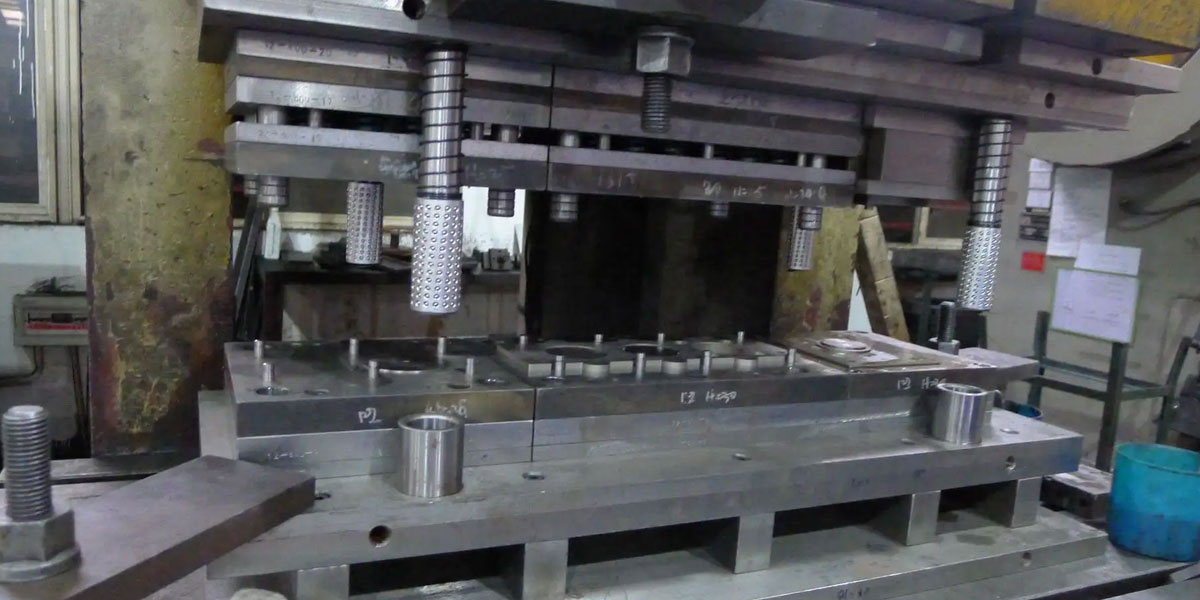
Aluminum deep drawing is a metal forming process used to transform flat sheet metal into complex three-dimensional shapes, such as cups, cans, enclosures, and automotive body panels. This process involves pulling a blank of aluminum through a series of dies and punches to gradually stretch and form it into the desired shape. The depth of the drawn part is typically greater than its diameter or width, hence the term “deep drawing.” This method is widely employed due to its ability to produce intricate parts with high precision and consistency.
Aluminum deep drawing differs from other metal forming techniques such as stamping and hydroforming in several key aspects. While stamping involves pressing a flat sheet of metal against a die to cut or shape it, deep drawing involves pulling the material into the die cavity to form complex shapes. Hydroforming, on the other hand, utilizes fluid pressure to force the metal into the desired shape. Unlike hydroforming, deep drawing does not require the use of a fluid medium, making it a more straightforward and cost-effective process for certain applications.
Aluminum deep drawing plays a crucial role in modern manufacturing across various industries, including automotive, aerospace, electronics, and consumer goods. Its significance lies in its ability to produce lightweight, yet durable components with excellent dimensional accuracy and surface finish. From automotive body panels to electronic enclosures, deep drawing enables the fabrication of parts that meet stringent performance requirements while offering design flexibility and cost-effectiveness.
Benefits Of Aluminum That Make It Ideal For Deep Drawing
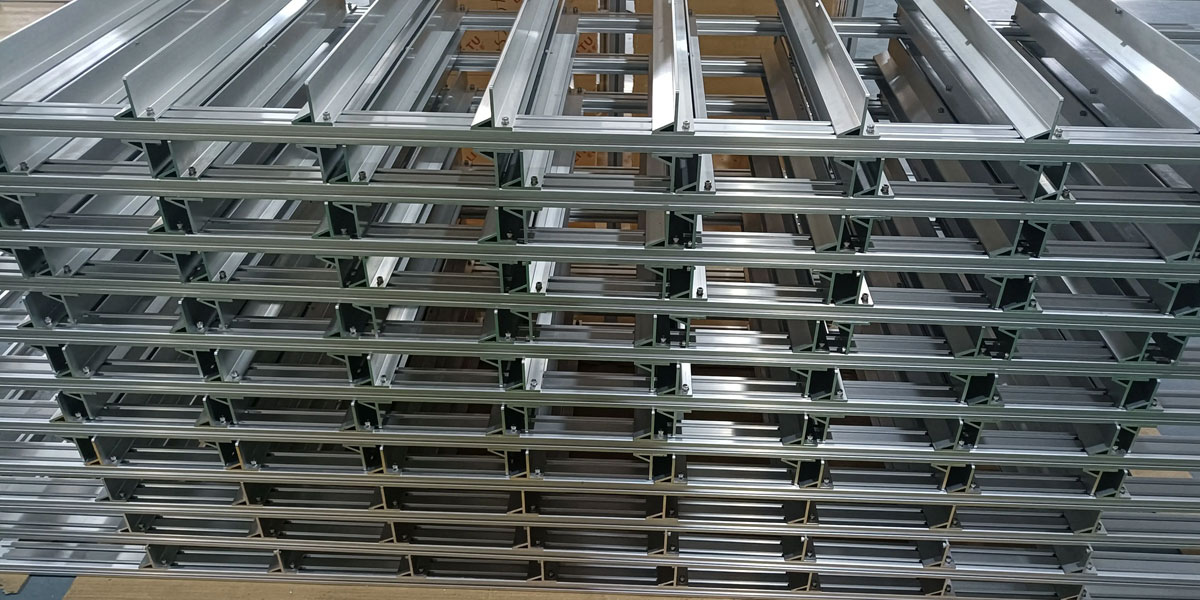
Aluminum possesses several unique properties that make it an ideal material for deep drawing applications. Here are some of the key benefits of aluminum:
Excellent Formability
Aluminum exhibits exceptional ductility, allowing it to undergo extensive deformation without fracturing or failure. This inherent formability makes aluminum well-suited for deep drawing processes, where complex shapes and intricate details are required.
Lightweight
Aluminum is significantly lighter than other metals such as steel, making it an attractive choice for applications where weight reduction is critical, such as automotive and aerospace components. The lightweight nature of aluminum helps to improve fuel efficiency, increase payload capacity, and enhance overall performance.
High Strength-to-Weight Ratio
Despite its lightweight nature, aluminum offers impressive strength characteristics, particularly when alloyed with other elements such as magnesium and silicon. This high strength-to-weight ratio allows aluminum components to withstand structural loads and stresses while minimizing overall weight, making it an ideal material for lightweighting initiatives.
Corrosion Resistance
Aluminum naturally forms a thin oxide layer on its surface, providing excellent corrosion resistance against moisture, chemicals, and environmental exposure. This inherent corrosion resistance ensures the durability and longevity of aluminum components, even in harsh operating conditions.
Good Thermal and Electrical Conductivity
Aluminum exhibits high thermal and electrical conductivity, making it suitable for applications requiring efficient heat dissipation or electrical conduction. This property is particularly advantageous in electronics, automotive heat exchangers, and electrical connectors.
Recyclability
Aluminum is highly recyclable, with the ability to be melted down and reprocessed repeatedly without significant degradation in quality or performance. This recyclability reduces the environmental impact of aluminum production and helps conserve natural resources, making it a sustainable choice for manufacturing processes.
Aesthetic Appeal
Aluminum offers a sleek and modern aesthetic, with a smooth surface finish and the ability to be easily coated or anodized in a wide range of colors and finishes. This aesthetic appeal makes aluminum an attractive choice for consumer electronics, architectural applications, and decorative products.
Cost-Effectiveness
Aluminum is cost-effective compared to other metals such as titanium and stainless steel, offering a favorable combination of performance, versatility, and affordability. The relatively low cost of aluminum raw materials, coupled with its ease of fabrication and processing, makes it an economically viable option for deep drawing and mass production.
The unique combination of formability, lightweight, strength, corrosion resistance, conductivity, recyclability, aesthetic appeal, and cost-effectiveness makes aluminum an ideal material for deep drawing applications across various industries. By leveraging the benefits of aluminum, manufacturers can achieve high-quality, lightweight components with complex geometries and superior performance characteristics.
Aluminum Grades For Deep Drawing
Aluminum Grade | Alloy Series | Key Features |
---|---|---|
1050 | 1000 | – Pure aluminum – Excellent formability – Good corrosion resistance – Low strength |
1100 | 1000 | – Pure aluminum – High electrical conductivity – Soft and ductile – Good weldability |
3003 | 3000 | – Alloyed with manganese – Moderate strength – High formability – Excellent corrosion resistance |
3004 | 3000 | – Alloyed with manganese – Higher strength than 3003 – Good formability – Suitable for beverage cans |
5052 | 5000 | – Alloyed with magnesium – Moderate to high strength – Excellent corrosion resistance – Suitable for marine applications |
6061 | 6000 | – Alloyed with magnesium and silicon – High strength and toughness – Good weldability – Suitable for structural components |
6063 | 6000 | – Alloyed with magnesium and silicon – Excellent extrudability – Good surface finish – Suitable for architectural applications |
Best Aluminum Grades For Deep Drawing Processes
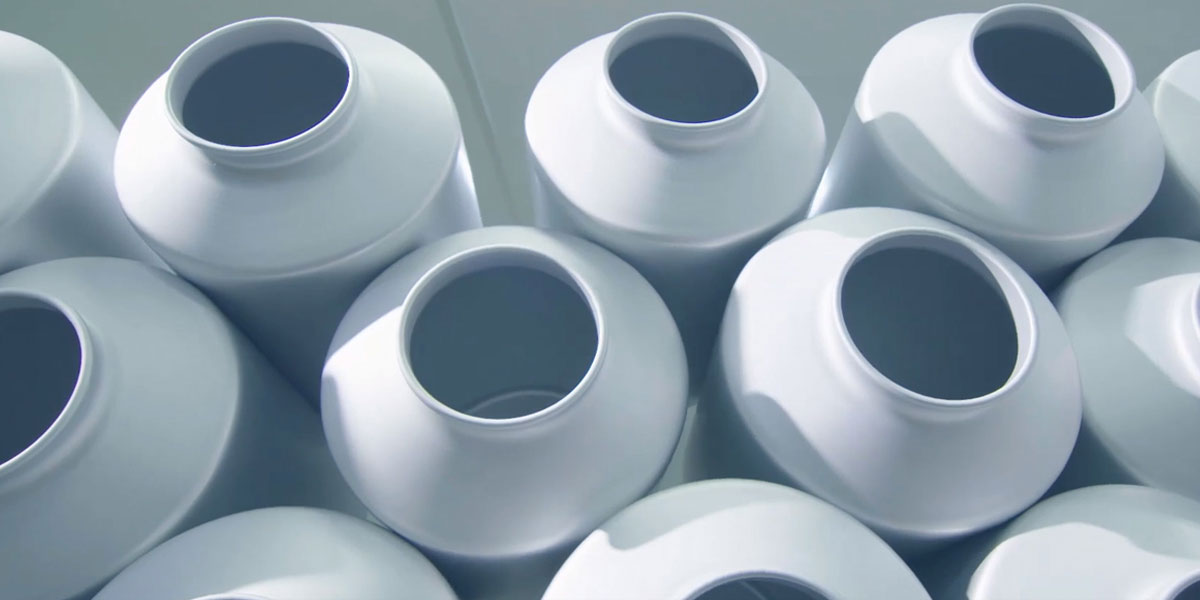
Choosing the best aluminum grade for deep drawing depends on various factors such as the specific application requirements, desired mechanical properties, and environmental conditions. Here are some aluminum grades commonly considered best for deep drawing processes:
3003 Aluminum Alloy
Alloyed with manganese, offering moderate strength and excellent formability.
Well-suited for deep drawing applications due to its high elongation and good resistance to corrosion.
Widely used in automotive components, kitchenware, and signage.
5052 Aluminum Alloy
Alloyed with magnesium, providing moderate to high strength and excellent corrosion resistance.
Offers good formability and is well-suited for deep drawing processes, especially in marine environments.
Commonly used in sheet metal fabrication for transportation, marine structures, and electronic enclosures.
5754 Aluminum Alloy
Alloyed with magnesium, offering excellent corrosion resistance and high strength.
Suitable for deep drawing applications requiring superior mechanical properties and resistance to atmospheric corrosion.
Frequently used in automotive body panels, fuel tanks, and chemical equipment.
6061 Aluminum Alloy
Alloyed with magnesium and silicon, providing high strength and good weldability.
Offers excellent formability and machinability, making it suitable for deep drawing and machining applications.
Commonly used in structural components, aerospace parts, and automotive fittings.
1100 Aluminum Alloy
Pure aluminum with excellent formability and ductility.
Soft and easy to work with, making it suitable for deep drawing processes requiring intricate shapes.
Often used in food packaging, lighting fixtures, and architectural applications.
3004 Aluminum Alloy
Alloyed with manganese, offering higher strength than 3003 with good formability.
Suitable for deep drawing applications, particularly in the manufacturing of beverage cans and containers.
Provides excellent corrosion resistance and weldability.
6082 Aluminum Alloy
Alloyed with magnesium and silicon, providing good machinability and corrosion resistance.
Offers excellent formability and weldability, making it suitable for deep drawing and machining processes.
Commonly used in structural components, machinery parts, and transportation equipment.
These aluminum grades offer a combination of formability, strength, and corrosion resistance, making them well-suited for deep drawing processes across various industries. However, the best choice depends on specific application requirements and production considerations. It’s essential to consult with materials engineers and conduct testing to determine the most suitable aluminum grade for a particular deep drawing application.
Common Aluminum Deep Drawing Techniques
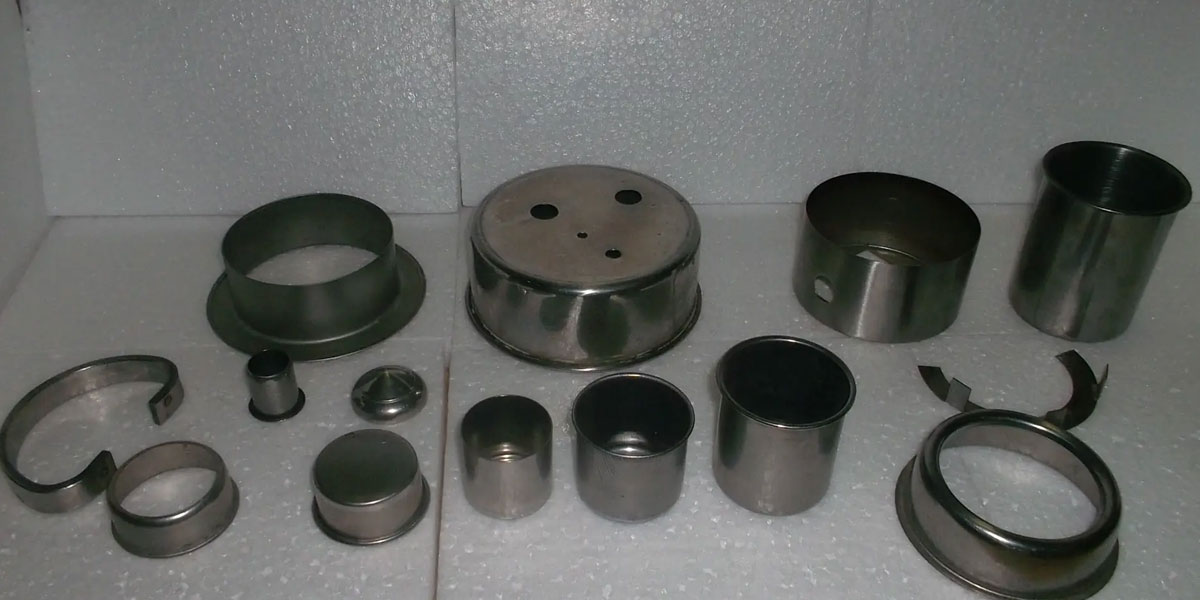
Several common aluminum deep drawing techniques are employed in manufacturing to shape flat sheets of aluminum into complex three-dimensional components. Here are some of the most common techniques:
Single-Draw Deep Drawing:
In this technique, a single blank of aluminum is drawn into a die cavity to form the desired shape.
The blank is held in place by a blank holder while a punch exerts force to pull the material into the die cavity.
Single-draw deep drawing is suitable for producing simple cylindrical or box-shaped components with uniform wall thickness.
Redrawing
Redrawing involves multiple drawing operations to achieve the final shape and dimensions of the component.
After the initial draw, the partially formed part may undergo one or more redraw operations to further stretch and refine the shape.
Redrawing is often used to achieve greater depth, tighter tolerances, and improved surface finish in deep drawn components.
Ironing
Ironing is a specialized deep drawing technique used to reduce the wall thickness of a drawn component while maintaining its length and diameter.
A punch with a smaller diameter than the die cavity is used to compress the walls of the drawn part, causing them to thin out and elongate.
Ironing is commonly employed in the production of cans, containers, and cylindrical components with thin walls and high length-to-diameter ratios.
Hydroforming
Hydroforming utilizes hydraulic pressure to shape aluminum blanks into complex geometries using a fluid-filled chamber instead of rigid tooling.
The blank is placed over a die cavity and sealed within a fluid-filled chamber, where hydraulic pressure is applied to force the material into the die.
Hydroforming allows for the production of components with intricate shapes, sharp corners, and varying wall thicknesses, often with reduced tooling costs and lead times.
Stretch Forming
Stretch forming involves stretching a flat sheet of aluminum over a die cavity using mechanical or hydraulic forces to form complex contours.
The material is clamped around the periphery of the die and stretched over the die cavity using a mechanical or hydraulic stretching mechanism.
Stretch forming is commonly used to produce curved or contoured components such as automotive body panels, aircraft fuselage sections, and architectural profiles.
Incremental Sheet Forming
Incremental sheet forming (ISF) is a versatile manufacturing technique that involves deforming a sheet of aluminum incrementally using a CNC-controlled tool.
A small, spherical-ended tool gradually shapes the material by applying localized forces, allowing for the production of complex geometries with minimal tooling requirements.
ISF is well-suited for prototyping, low-volume production, and the fabrication of customized components with varying geometries.
These techniques can be adapted and combined to meet the specific requirements of different applications, allowing manufacturers to produce a wide range of aluminum deep drawn components efficiently and cost-effectively.
Process Optimization and Control in Aluminum Deep Drawing
Manufacturers and product engineers often encounter setbacks in aluminum Deep Drawing regardless of its remarkable machinability. This section discusses some of these challenges along with possible solutions:
Design for Deep Drawing
Guidelines for Part Design:
- Uniform Wall Thickness: Maintain consistent wall thickness throughout the part to ensure even material flow and reduce the risk of defects such as thinning or wrinkling.
- Smooth Transitions: Avoid sharp corners and sudden changes in geometry that can cause stress concentrations and material deformation. Use fillets and radii to create smooth transitions between features.
- Draw Ratios: Ensure appropriate draw ratios to prevent excessive thinning or stretching of the material. Aim for a draw ratio (Diameter of blank / Diameter of final part) of 2:1 or less for optimal formability.
- Blank Size: Use blanks that are slightly larger than the final part dimensions to allow for material flow and avoid wrinkles or tearing during drawing.
Utilizing Simulation Software:
- Finite Element Analysis (FEA): Use FEA software to simulate the deep drawing process and predict potential defects or areas of concern. This allows for virtual prototyping and optimization of part design before physical tooling is produced.
- Material Models: Incorporate accurate material models into simulation software to accurately predict material behavior under various loading conditions, helping to optimize forming parameters and minimize defects.
Process Parameters and Control
Key Variables Affecting Deep Drawing Quality:
- Blank Holder Force: Control the force applied to the blank holder to maintain uniform material flow and prevent wrinkling or thinning of the material.
- Draw Ratio: Adjust the draw ratio to achieve the desired deformation without exceeding the material’s limits. Higher draw ratios may result in increased thinning, while lower draw ratios may lead to wrinkling or tearing.
- Draw Speed: Optimize draw speed to balance productivity and part quality. Higher draw speeds may increase productivity but can also lead to increased springback and reduced dimensional accuracy.
Monitoring Techniques:
- Strain Analysis: Use strain gauges or optical strain measurement systems to monitor material deformation during the drawing process. Analyzing strain distribution can help identify potential defects and optimize process parameters.
- Force Sensors: Install force sensors in the press to measure the forces acting on the tooling during deep drawing. Monitoring these forces allows for real-time adjustment of process parameters to maintain consistent part quality.
- Real-Time Process Control: Implement closed-loop control systems that use feedback from monitoring sensors to adjust process parameters such as blank holder force, draw ratio, and draw speed in real time, ensuring consistent part quality throughout production.
Strategies for Minimizing Springback and Achieving Dimensional Accuracy:
- Backward Compensation: Adjust tooling dimensions and process parameters to compensate for anticipated springback during deep drawing. This involves overforming the part slightly to account for elastic recovery after forming.
- Optimized Die Design: Design dies with features such as draw beads, stretch zones, and variable radii to control material flow and minimize springback. Use progressive die designs for complex parts to minimize secondary operations and dimensional variability.
Quality Assurance and Inspection
Inspection Methods for Detecting Defects:
- Visual Inspection: Perform visual inspections of drawn parts to detect surface defects such as wrinkles, splits, and thinning. Use magnification tools or automated vision systems for detailed inspection of complex geometries.
- Dimensional Inspection: Measure critical dimensions of drawn parts using precision measurement tools such as calipers, micrometers, or coordinate measuring machines (CMMs) to ensure dimensional accuracy and conformance to specifications.
Non-Destructive Testing Techniques:
- Ultrasonic Inspection: Use ultrasonic testing to detect internal defects such as porosity, cracks, or inclusions in drawn parts. Ultrasonic waves are transmitted through the material, and deviations in wave propagation indicate the presence of defects.
- Eddy Current Inspection: Employ eddy current testing to detect surface and near-surface defects in conductive materials such as aluminum. Eddy currents induced in the material interact with defects, causing changes in impedance that can be detected and analyzed.
- X-ray Inspection: Utilize X-ray imaging to inspect internal features and detect defects such as voids, inclusions, or dimensional inaccuracies in drawn parts. X-rays penetrate the material, allowing for non-destructive evaluation of internal structure and defects.
Implementing Statistical Process Control (SPC):
- Process Monitoring: Use statistical process control (SPC) techniques to monitor key process parameters such as blank holder force, draw ratio, and dimensional accuracy during deep drawing operations. Track process variation over time to identify trends and deviations from established control limits.
- Root Cause Analysis: Analyze process data to identify root causes of defects or variations in part quality. Implement corrective actions to address underlying issues and prevent recurrence of defects.
- Continuous Improvement: Establish a culture of continuous improvement by using SPC data to drive process optimization and quality enhancement initiatives. Implement feedback loops to ensure that lessons learned from process monitoring are incorporated into future production cycles.
By focusing on design optimization, process control, and quality assurance techniques, manufacturers can improve the efficiency, consistency, and quality of aluminum deep drawing processes, ultimately enhancing product performance and customer satisfaction.
Applications Of Aluminum Deep Drawing Parts
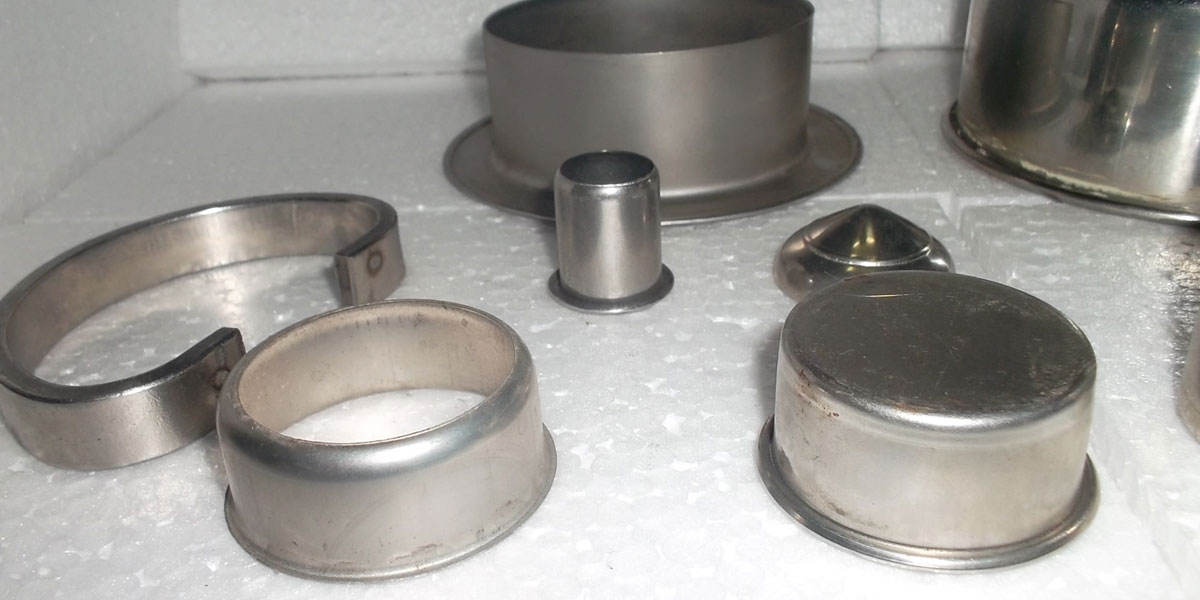
Aluminum deep drawing parts find extensive applications across various industries due to their lightweight, durability, and versatility. Here are some common applications of aluminum deep drawing parts:
Aluminum Deep Drawing For Automotive Industry:
- Body Panels: Aluminum deep drawing parts are used in automotive body panels such as hoods, doors, fenders, and trunk lids due to their lightweight properties and corrosion resistance.
- Heat Exchangers: Components such as radiator tanks, condenser headers, and intercooler end tanks are often manufactured using aluminum deep drawing for their thermal conductivity and formability.
- Fuel Tanks: Aluminum deep drawing is used to fabricate fuel tanks for automobiles, motorcycles, and recreational vehicles due to aluminum’s lightweight and corrosion-resistant properties.
Aluminum Deep Drawing For Aerospace and Aviation:
- Aircraft Fuselage Parts: Aluminum deep drawing is employed in the production of aircraft fuselage parts such as stringers, bulkheads, and window frames due to its high strength-to-weight ratio and formability.
- Engine Components: Parts like inlet manifolds, housings, and brackets in aircraft engines are often manufactured using aluminum deep drawing for their lightweight and high temperature resistance.
Aluminum Deep Drawing For Electronics
- Enclosures: Aluminum deep drawing parts are widely used in electronic enclosures for devices such as smartphones, laptops, tablets, and cameras due to their lightweight, durability, and electromagnetic shielding properties.
- Heat Sinks: Aluminum deep drawing is utilized to manufacture heat sinks for electronic components such as CPUs, GPUs, and power transistors, providing efficient heat dissipation and thermal management.
Aluminum Deep Drawing For Consumer Goods
- Cookware: Aluminum deep drawing parts are commonly used in the production of cookware such as pots, pans, and baking dishes due to aluminum’s excellent thermal conductivity and lightweight properties.
- Lighting Fixtures: Aluminum deep drawing is employed in the manufacturing of lighting fixtures such as lamp housings, reflectors, and shades due to aluminum’s corrosion resistance and formability.
- Household Appliances: Components such as appliance housings, door panels, and handles in household appliances like refrigerators, washing machines, and dishwashers are often manufactured using aluminum deep drawing for its lightweight and aesthetic appeal.
Aluminum Deep Drawing For Medical Devices
- Implantable Devices: Aluminum deep drawing parts are used in the production of implantable medical devices such as pacemakers, orthopedic implants, and surgical instruments due to aluminum’s biocompatibility and corrosion resistance.
- Diagnostic Equipment: Components for medical diagnostic equipment such as X-ray machines, MRI scanners, and ultrasound transducers are manufactured using aluminum deep drawing for their lightweight and structural integrity.
Aluminum Deep Drawing For Packaging
- Containers: Aluminum deep drawing is used to manufacture containers for packaging food, beverages, cosmetics, and pharmaceuticals due to aluminum’s impermeability to light, moisture, and gases, as well as its recyclability.
- Closures: Caps, lids, and closures for bottles, jars, and tubes are often produced using aluminum deep drawing for their tamper-evident sealing and barrier properties.
These are just a few examples of the wide-ranging applications of aluminum deep drawing parts across industries. With advancements in material science and manufacturing technologies, the use of aluminum deep drawing continues to expand into new and innovative applications, driving efficiency, performance, and sustainability in product design and manufacturing.
How To Choose The Right Partner For Aluminum Deep Drawing
Having gone through this article, you should have realized that aluminum offers many desirable benefits and properties with Deep Drawing. However, choosing the ideal manufacturing partner to handle your aluminum Deep Drawing project is essential.
As such, it is advisable to partner with a stamping shop with the right machining tools to fabricate quality aluminum parts with high accuracy. Additionally, the stamping service provider must have experience manufacturing aluminum parts and all the required quality certifications to ensure your parts meet the required quality standards.
However, it is not advisable to partner with a deep drawing shop without the required quality certification and punch machines to achieve the desired precision and accuracy. Similarly, you should not outsource your custom aluminum parts to a partner with little or no experience handling such projects!
Be-Cu stamping company is here for you whenever you need aluminum volume manufacturing or custom aluminum stamping parts for your applications. We are a leading deep drawing expert with a team of qualified and experienced engineers. We leverage our aluminum deep drawing expertise to offer stamping parts with tight tolerances and faster cycle time. Contact us now to get a quote for your project!